Legacy
THE INCEPTION — When India’s Metallurgical Journey Took Shape
The National Metallurgical Laboratory (NML) was among the first five laboratories (along with the National Chemical Laboratory, the National Physical Laboratory, the Fuel Research Station, and the Glass & Ceramics Research Institute), envisioned to be set up under the aegis of Council of Scientific and Industrial Research (CSIR), for fuelling India’s industrial growth. CSIR in itself came into existent on 26th September 1942 and in the year 1943, the governing body of CSIR approved the proposal of establishment of these five laboratories in strategically suitable locations across the country. The foundation stone of NML was laid in the year 1946, by the Minister for Education and Arts in the Interim National Government Hon’ble Sri Chakravarti Rajagopalachari on 21st November 1946 marking a major milestone in the metallurgical history and heritage of the country. NML was inaugurated in the year 1950 by then prime minister of the Republic of India, Pandit Jawaharlal Nehru, embodying hope for the future. NML was part of Sri Shanti Swaroop Bhatnagar’s vision or creating a network of research institutions to advance India in science and technology.
Established just after India's independence on 26th November 1950, NML has been crucial in developing country's capabilities in the areas of minerals, metals, and materials through scientific research, technology development, industrial services, and human resource development. Since its establishment, NML has broadened its research to include extractive metallurgy, alloy development, metallurgical process modelling, minerals research, advanced materials, integrity evaluation, surface engineering, and sustainable metals production. The illustrious legacy in the various fields encompassing the minerals, metals, and materials has been highlighted below.
FERROALLOYS — A Silent Force Behind Stronger Steel
The development of ferroalloys was crucial for the growth of India’s iron and steel industry. NML began producing low-carbon and carbon-free ferrochrome via the aluminothermic route to support ordnance establishments. Special focus on ferroalloys began in the Third Five Year Plan of NML. NML's 500 kVA submerged arc furnace (SAF), India’s first, marked the start of serious ferroalloy production in the country (1962). This furnace became a key facility for ferroalloy producers and was also used for general ore smelting. Since the 1960s, NML made significant contributions to the ferroalloy industry. In 1975–76, it produced calcium-silicide for the first time in India, which met ISI standards and was sent to Hindustan Machine Tools (HMT) and Heavy Engineering Corporation (HEC). Industrial-scale trials for vanadium-rich slag were also conducted. NML's long-standing collaboration with Ferroalloys Corporation (FACOR) led to the establishment of a 12 MVA furnace for high-carbon ferrochrome and an 8 MVA furnace for low-carbon ferrochrome in 1967. FACOR supported several investigations, including the use of ferrochrome slag in foundries and the use of magnesium metal waste for inoculants. In late 1960s, NML also developed India’s first technology for production of low-carbon ferro-chrome containing up to 0.05-0.2 % carbon and carbon-free ferro-chrome for use in alloy steels.
Progressing with the legacy, NML, in recent years, has developed a process for carbon-free ferrovanadium (Fe-V) preparation through an aluminothermic route from vanadium pentoxide concentrate. The aluminothermic reaction is carried out in a refractory lined chamber. The fluxing agents are mixed with vanadium pentoxide and the required amount of aluminium and iron oxide. The process for the silico thermic reduction of Mn ore is developed on a laboratory scale at NML to produce low-carbon ferromanganese. NML has also developed a process for utilising CO2 as a decarburising agent to reduce the carbon content in high-carbon ferromanganese, which can be used for producing high-strength, low-alloy (HSLA) steels or advanced high-strength steels (AHSS) etc.
SPONGE IRON —Soft Metal with Strong Intent
The use of coal and low-grade fuels in sponge iron production was crucial for developing India's steel economy and replacing scrap in electrical steelmaking. In line with the research priorities of the Planning Commission and Ministry of Steel, a rotary kiln facility (200–300 kg/h) was established for larger-scale sponge iron trials. The then Union Minister of Steel, Shri Charanjit Singh Yadav, praised NML's efforts, stating, “National Metallurgical Laboratory has shown exemplary courage in taking up the challenging initiative for promoting the direct reduction techniques in the production of sponge iron. This can result in establishing a large number of mini steel plants in the country, which will serve the steel requirements of the areas nearby, utilising, wherever possible, the deposits of iron that are available locally. These mini steel plants, using sponge iron technique, will be able to provide 20–25% of the steel requirements in the years to come.”
Iron ores from various organisations, including iron ores from Industrial Development Corporation of Odisha Limited (IDCOL), Bhilai Steel Plant, State Industrial Investment Corporation of Maharashtra (SIICOM), Andhra Pradesh Industrial Development Corporation (APIDC) and National Mineral Development Corporation (NMDC), were tested in the rotary hearth furnace for sponge iron production. Under a UNIDO-sponsored study, reduction tests were also conducted on Aswan (Egypt) ore, marking NML's first international research project. Another study, sponsored by the Nepal Bureau of Mines, tested their raw materials. India’s first commercial sponge iron plant, with a capacity of 25,000–30,000 tonnes per year, was established at Andhra Cement Company in Vijayawada (1975–76) using NML's solid reduction technology. Dr. Ing. H. P. Mishra, former Chairman of IPICOL, acknowledged NML's contribution in 2010: “From 1970 to 1974, I sought NML's expertise for our sponge iron and Ferro-vanadium project, which helped us understand the Orissa and Tata Sponge Iron projects.”
Recently, CSIR NML developed the process for the production of DRI using iron ore slime, mill scale, and non-coking coal in a tunnel kiln that has been transferred to M/s. SMRW, Ranchi for Commercial Production. DRI Produced has good Metallization (> 88%) and is suitable for BOF, IF and EAF furnaces for Steel Making. The steel industry is regarded as the most critical industry in the nation and is crucial to economic prosperity. NML has been working on green steel making from hydrogen-based directly reduced iron (H-DRI) on a laboratory scale. Besides hydrogen, ammonia is also being used as a reducing agent for the reduction of iron ore pellets, wherein H-DRI has been used in green steel making in induction furnaces/Electric Arc furnaces.
MAGNESIUM Matters — NML Made it Happen in India
A key milestone in the early seventies was the commissioning of the Magnesium Plant and the successful trial runs. The first sponge magnesium was produced in the laboratory in the late 1960s, with Mr. M. P. Menon leading the team that produced the country’s first magnesium ingot. The magnesium pilot plant was commissioned in February 1972 and was inaugurated by Sri Mohan Kumaramangalam, Union Minister for Steel and Mines, in November 1972. High-purity magnesium (99.9%) was produced in tonnage quantities, and sponge magnesium was successfully melted and alloyed at a pilot scale. The magnesium of required purity standards was produced during the development period was supplied to various strategic and commercial organizations, including Ordnance Factories, Hindustan Aeronautics Limited, the Government Mint, Bharat Aluminium, Heavy Engineering Corporation, Vikram Sarabhai Space Centre, Defence Research Laboratories, and the Nuclear Fuel Complex. These users confirmed that the magnesium met the required purity standards, enabling them to replace imported magnesium. Later, the plant was transferred to Southern Magnesium (SMCL, Rajmundary) in August–September 1987, making it the sole magnesium producer in the country for over a decade. This also led to Mg alloy development for strategic needs of country.
During 2000-2017, CSIR-NML started development of Electrothermal pilot plant with liquid state silicothermic reduction technologies. Since 2020, CSIR-NML re-visited its Pidgeon/Retort process and a single retort prototype for 14-15 kg feed/charge and 2.5-3.0 kg Mg metal is being successfully established. For refining Mg and scrap-recycling, vacuum distillation-based technologies were developed with indigenous equipment-designs.
Since May 2024, CSIR NML started a piloting activity aimed to establish a pilot plant for commercial grade as well as high pure magnesium metal from Indian dolomite resources/scraps under ambit of CSIR Special Project Scheme-Pilot Plant (CSPS-PP). The proposed pilot plant is planned for 120-150 kg Mg metal/day (600 Kg feed/ ~2 TPD feed of dolomite basis). It is envisaged with integration of NML’s improved-retort/Pidgeon technology and continuous vacuum distillation refining technology, with an aim to lower c-footprint, circular economy through slag valorization and inbuilt Mg scrap recycling capabilities for high purity magnesium.
High-Temperature Materials Frontier: Decades of CREEP Excellence
Creep testing at the NML began modestly in the early 1960s with just 12 machines, initially supporting laboratory research in indigenous high-temperature alloy development. However, by the late sixties, the need for a central, large-scale creep testing facility became evident. At that time, India was heavily reliant on imports for creep-resistant steels, as the lack of indigenous creep data deterred users from adopting domestically produced materials. Recognizing this gap, a consortium of stakeholders—including steel producers (like SAIL and Mahindra-Ugine), users (such as BHEL), R&D organizations (NML and RRC-Kalpakkam), and statutory bodies (then ISI, DGTD)—came together in the mid-sixties to recommend the creation of a national-scale creep testing infrastructure.
This culminated in the establishment of Asia’s largest creep laboratory at NML in 1972, with 150 test points supported by equipment donated by UNIDO. The facility marked a significant milestone in NML's history and catalysed a nationwide effort to indigenize creep-resistant steels. Under the guidance of the Indian Creep Panel—a voluntary body with NML as its secretariat—an indigenous development program was launched. This initiative successfully rationalized steel specifications, designed robust test programs for qualification, and enabled commercial production followed by long-term creep evaluation of domestically developed alloys. Key steel grades indigenized included high-temperature bolting steels (CrMoV with and without Ti, B, EN20), superheater tubing steels (1CrMo, 2¼Cr1Mo, 2CrMoV), and forging grade steels (CrMo, CrMoV). NML generated up to 30,000 hours of creep data on these steels and benchmarked them against international standards. The evaluations led to the Central Boiler Board approving the use of these indigenous steels in Indian power plants. By 1980, NML had firmly established itself as a national hub for creep testing, materials qualification, and failure analysis. Long-term testing for BHEL continued, while NML played a pivotal role in qualifying materials for the Fast Breeder Reactor Program at the Reactor Research Centre (now Indira Gandhi Centre for Atomic Research, IGCAR). NML holds the distinction of conducting India’s longest creep test—lasting 140,000 hours—on stainless steels for the Fast Breeder Reactor at IGCAR, Kalpakkam.
NML's extensive expertise also enabled it to lead the remaining life assessment (RLA) of high-temperature components from thermal power plants, petrochemical units, and fertilizer industries. These investigations helped extend the operational life of critical equipment. Through decades of microstructural analysis, failure case studies, and long-term testing of both service-exposed and lab-tested samples, NML has built a substantial repository of data valuable for life prediction and extension of industrial components. Even today, NML continues to serve major national materials development programs. It remains a recognized authority in creep testing, RLA of high-temperature components, and IBR certifications, contributing significantly to the strategic needs of the country’s infrastructure and energy sectors.
COLUMN FLOTATION - Purifying Resources, Powering Industry
CSIR - National Metallurgical Laboratory (CSIR-NML) has been at the forefront of indigenizing the ‘Column Flotation Technology’ for processing lean grade and fine-grained ores for over three decades. Laboratory-scale (74 mm diameter) and Pilot plant-scale (500 mm diameter) flotation columns were designed, fabricated, and field-tested at various private and public sector mineral processing industries nationwide. Development of column flotation technology achieved Technology Readiness Level - 9, implying that it is ready for successful deployment at a commercial scale. The USP of CSIR - NML is that it provides a one-stop solution for the installation and commissioning of commercial-scale flotation columns by collaborating and partnering with an EPC company, M/s Tega McNally Minerals Limited, Bengaluru, and reagents manufacturers and suppliers, M/s Sudarshan Chemical Industries Limited, Pune. So far, five laboratory-scale, two pilot plant-scale, and eight commercial-scale flotation columns have been commissioned to beneficiate limestone, barite, and fine coal recovery.
LOW SHAFT - High Ambitions
A 15-tonne/day pilot low-shaft furnace, one of the largest pilot plants established anywhere in the world, was operational at NML since 1959. The plant, costing close to 3 million (in mid-1950s) and supplied by the Demag-Humboldt Niederschachtofen, Duisburg, West Germany took nearly two years for construction. It required 100 tonnes of materials handling per day! The objective of having the plant was to assess the possibilities of making commercial grades of pig iron with raw materials like soft iron ores, iron ore fines, beneficiated magnetite iron ore, with various non-coking high ash coals or carbonized lignite, plentiful supplies of which exist in India but unsuitable for exploitation in conventional blast furnaces. This plant yielded the first pig iron in India from iron ore fines and coal with over a thousand tons of foundry grade pig iron was produced in 1959 itself. There were five phases of trials: 1) Use of low grade ores and coal; 2) Charge of self-fluxing briquettes from iron ore fines, limestone and non-coking coals; 3) Utilization of carbonized lignite from Neyveli & Palamu & utilisation of Salem magnetite; 4) Improving fuel economy through top gas injection, sintered burden and oxygen enrichment of blast and 5) Production of ferro-alloys such as Fe-Mn and Fe-Cr. More than seventy campaigns were conducted over two decades on round the clock basis to establish technical and economic feasibility of producing pig iron using raw materials from all across the country. The results of these studies, which were carried out under a large number of sponsored studies, notably from the state governments of East Punjab, Andhra Pradesh, Rajasthan, Maharashtra, Tamil Nadu and Bihar were used for the establishment of small units for iron and steel production in different parts of India. Government of Nepal sponsored a study to establish a small-scale iron production facility using their raw materials. Pilot scale tests in the low shaft furnace were also conducted on smelting of manganese ores to produce ferromanganese, titaniferous ores for TiO2 slag and phosphate ore for ferro-phosphorous.
The production of pig iron from iron ore and coal unsuitable for iron production by conventional blast furnace symbolised great foresight. Oxygen enrichment and direct injection of liquid naphtha were introduced in the original design to improve energy economy. The environmental sustainability of the process was further improved by the development of processes for the utilisation of slag for ballast, production of light weight aggregate for insulation concrete and blended cement as a replacement for the ordinary Portland cement. The plant which was the workhorse of NML until the sixties was sold to M/s Polybond Co. in Durg, Raipur which is operational even today.
In STEEL We Trust
Since its inception, CSIR-NML has significantly contributed to the development of indigenous steel making technologies and new product development, thus reducing the country’s dependency on imports and foreign know-hows. Around thirty per cent of steel in India was produced by secondary producers using induction furnaces, often resulting in high phosphorus content. In its early years, CSIR-NML, with AIIFA and the Ministry of Steel, developed a flux to reduce phosphorus levels to meet BIS standards, with promising industrial test results. Efforts are still ongoing to refine the flux for various other refinement purposes.
Oxygen lancing for efficient and clean steelmaking was first introduced in Indian steelmaking industries during the 1950s to early 1960s. In a noteworthy contribution in the year 1957-58, NML set up first pilot plant facility of oxygen lancing in the scale of 0.1 ton for R&D activities in the quest to generate data which were envisaged to be helpful in the country’s steel expansion programme.
The continuous casting plant on pilot scale was first designed and fabricated at NML in 1961. A double- walled, water-cooled copper die with the exit water falling directly on the cast rod in the form of a spray was used for casting aluminium and its alloys. The size of the copper die was 31.75 mm inner diameter and 50.8 mm long. The speed of casting was around 457.2 mm/min with a circulating water rate of 3500 cc/min. This was probably the first continuous die casting unit in India. Although the continuous casting process was conceived by Bessemer in 1858, the continuous casting of steel did not gain widespread widespread use until the 1960s.
NML’s work in the area of developing nickel-free stainless steel, named THACKERON, after the Director General of CSIR at that stage, was a major breakthrough. This invention can be considered way ahead of its time due to Nickel’s strategic nature and present volatile market. The first foreign patents were granted to NML on the methods of producing these new steels (French Patent 1208393: September, 1959; UK Patent 833308, August, 1960).
The development of Ni-free substitute steels was not restricted to only the austenitic stainless steel. Another achievement in the development of Ni-free steels was the development of technology for substitute Ni and Co free electrical resistance heating elements which was transferred to M/s New Horizon, Pondicherry. Ni-free creep resistant austenitic steels were developed for exhaust valves for TATA D1 engine as well as Diesel Locomotives and the know-how was transferred to M/s Star Wire (India) Ltd. New Delhi in 1993.
Current research focuses on advanced automotive steels and the reuse of iron and steel plant wastes for value-added products. Over the past decade, a team of Scientists at CSIR-NML has made substantial contributions in indigenous development of steels through an innovative and energy-efficient Quenching and Partitioning (Q&P) heat-treatment technology. They have designed novel cost-effective steel compositions for various applications with an aim to reduce the import of high-end, value-added steel products. A pioneering scientific approach, coupled with strategic lab-scale implementation, has paved the way for pilot trial and industrial-scale steel production. These achievements were acknowledged by Tata Steel, which stated “This kind of high strength steel may be the first attempt through hot strip mill in India. The project is a true example of translatory research from Lab scale to Commercial scale.” These efforts have resulted in 2 technology development and over 5 patents. The ongoing efforts are focused on further utilizing the potential of this advanced technology (Q&P) to develop high-performance steels for armour, automotive, pipeline, etc. applications.
Recent activities in steel develop at NML also include development of high-performance rail steels for upcoming high-speed rails for the country. With the help of novel in-house developed thermodynamic models, new alloys were designed for formation of nano-pearlitic microstructure (with interlamellar spacing in the range of 80-95 nm). Importantly, the concept of non-partitioned nano-pearlite has been reported for the first time ever, wherein substitutional elements are retained within the soft ferrite phase leading to solid solution strengthening aiding enhancement in yield strength. These steels were observed to possess much higher strength, hardness and wear resistance as compared to conventional rail grades used in India. The optimized product has been patented as ‘Ultra High Strength Hypereutectoid Nano-Pearlitic Steels (Granted Indian Patent# 515907)’.
In another recent contribution, scientists at NML developed novel super-martensitic stainless steel compositions and their processing technology for space application. This development focused on improving the cryogenic impact properties of cast alloys for components such as the turbo fuel pump, which must endure high impact and cavitation at extremely low temperatures (around -196 °C). Given that investment cast alloys offer no scope for property modification through thermo-mechanical treatment, the challenge was to enhance performance solely through alloy and process design. A tailored approach was adopted involving alloy design and optimization, followed by meticulous process design. An alloy with both high yield strength and excellent impact resistance at cryogenic temperatures was successfully developed. The final composition and corresponding heat treatment cycle developed have been adopted and implemented by VSSC-ISRO at component-level, marking a significant advancement in indigenous material capability for strategic applications in the Indian space program.
URBAN MINING — Recycling E-WASTE for a Cleaner Tomorrow
CSIR-National Metallurgical Laboratory (NML), Jamshedpur emerged to be pioneer in the development of application-oriented e-waste recycling processes, fulfilling zero waste concepts. Since early 2000s, the group of scientists at NML has been working for development of process to recuperate non-ferrous metals from printed circuit boards (PCBs), rare earth metals from various types of magnets and precious metals from e-waste in an organized manner by recycling various e-wastes. In order to carry out scale-up and pilot scale trials, a centre dedicated for the development of feasible technologies to recover non-ferrous, precious and rare earth metals from secondary resources has been established. Dr. Shekhar C. Mande, Director General of CSIR and Secretary of the Department of Scientific and Industrial Research (DSIR), Govt. of India inaugurated this centre named as Urban Ore (E-waste) Recycling Centre (UORC) at CSIR-NML, Jamshedpur, on 20th April 2019. Under this banner, CSIR-NML has recently transferred 14 technologies to various Indian recycling companies with high Customer Satisfactory Index. The transfer of technologies is a great step towards the "Swachhata Abhiyan" initiated by Government of India.
The developed processes are fully indigenous, economically feasible, less energy intensive and receive high value of metals and materials. E-waste recycling will generate new market for precious, non-ferrous, rare earth metals recovery by gaining high revenue due to less process cost, gain of high value recycled metals/ materials and techno-economical. The e-waste recycling sector will contribute to the country's economy and create employment. In future, the segments of technology will be available to common people as cottage industries/ manufacturers supported small scale industries in environmentally friendly manner.
In recent years CSIR-NML has contributed a lot in the area of development of feasible process for recycling of e-waste to reclaim the metals, materials and valuables which are as follows:
- Recovery of Precious metals (Au, Ag, Pt, Pd) from scrap telecommunication devices, Medical equipment’s, Key Boards, and Printed Circuit Boards (PCBs) of various E-waste
- Recovery of Lithium, Cobalt, Copper, Nickel, Manganese and recyclable Graphite from waste Li-ion (LIBs) and Ni-Metal Hydride (NiMH) batteries
- Recovery of Rare earth metals (Nd, Sm) from various Magnets of Wind Turbine and E-waste
- Recovery of Rare earth metals (Nd, Ce and La) from electric vehicle (Ev) batteries
- Recovery of Rare earth metals (Y, Eu, La, Ce and Tb) from waste Fluorescent Lamps
- Recovery of Strategic metal Germanium (Ge) from Telecom Optical cables and Solar Panels.
Under the banner of UORC, CSIR-NML has recently transferred e-waste recycling technologies to various industries (M/s Novasensa Pvt. Ltd., New Delhi., M/s Recyclib Pvt. Ltd., Delhi., M/s Metaore Recycler Pvt. Ltd., Kolkata., M/s NILE Li-Cycle Pvt. Ltd., Hyderabad., M/s Jai Mata Di Plastics, New Delhi., M/s Evergreen Recyclekaro Pvt. (India) Ltd., Mumbai; M/s EXIGO Recycling, New Delhi; M/s SBCON Recycling Pvt. Ltd., Ahmedabad; M/s ADV Metal Combine Pvt. Ltd., Durg; M/s UNQ IND Pvt. Ltd., Firozabad; M/s Eco Recycling Company, Mumbai) for the recovery of rare, rare-earth, precious and strategic metals. This initiative will create self-employment, entrepreneurship and promote cottage industries. In this pursuit, scientists from CSIR-NML have been conferred several awards including CSIR Technology award (2021), NM Sampat Award (2021), RECOM Award (2012), etc.
MINERAL BENEFICIATION- From Earth to Industry
The heavy integrated Mineral Beneficiation Pilot Plant, built at a cost of ₹ 5 million (in the early 1960s) as a part of the Third Five Year Plan was inaugurated in early 1963 by Prof. Humayun Kabir, the then Union Minister for Scientific Research & Technical Education. The plant was meant for round the clock operation to develop basic data for beneficiation of raw materials. The plant had a capacity to treat up to 5 tonne of ore per hour depending upon the specific treatment and optimum upgrading cycle and was one of the best equipped integrated plants in the world for undertaking beneficiation and up-gradation of low-grade ores and minerals and for trials pertaining to agglomeration of concentrates. The equipment was procured with funds provided by the US Export-Import Bank. The entire engineering design, layout, erection and installation of this pilot plant were done by the staff of the National Metallurgical Laboratory. The plant was capable of continuously treating any type of ore by classical ore-dressing methods including reduction roast treatments and agglomeration of concentrate fines. The plant was rated to be one of the best internationally. Sir Charles Goodeve, Director, British Iron & Steel Research Association, during the inauguration of the plant stated:
“I had the opportunity of studying quite a number of pilot plants in my life but I had not yet seen any that can stand above the pilot plants in operation at the NML… the British Iron & Steel Research Association who were planning to extend their mineral beneficiation pilot plant facilities had not even gone half the pace in comparison with NML during the last five years. I am seriously thinking of sending some of our own problems which could be worked out at the NML where the facilities in many respects exceed greatly our own in Britain”
The plant was extensively used for mineral beneficiation studies; especially iron ore, limestone, dolomite, manganese ores, complex sulphide ores of base metals, graphite, coal, kyanite, wolframite, magnesite, barites, apatite, phosphate and fluorspar. Almost the entire steel industry of India (TISCO, IISCO, SAIL) used the basic data generated by NML to develop the flow sheet required for iron ore beneficiation and agglomeration of iron ores. Similarly, both the major copper plants of Hindustan Copper at Ghatsila and Malanjkhand adopted the flow sheets developed by NML for the production of copper concentrates. Several of the graphite beneficiation plants and the fluorspar plants in India owe their existence to NML. The plant upgraded in 1998, has contemporary facilities. Today, Mineral Processing Division of National Metallurgical Laboratory can boast of over 800 sponsored investigations to its credit covering almost the entire spectrum of ores and minerals including coal. Major beneficiaries included Tata Iron & Steel Co. Ltd., all the steel plants under Hindustan Steel Ltd. [now Steel Authority of India Ltd. (SAIL)], Mineral Development Corporation of Gujarat, Rajasthan, Tamilnadu, Andhra, Bihar and several other states, Hindustan Copper Ltd., National Mineral Development Corporation, Indian Rare Earth Ltd. and many others. The list also includes several overseas clients from Nepal, Bhutan, Thailand, Kazakhstan, Syria, Egypt and United Kingdom.
Strategic Metals Extraction- Efforts Towards Resource Sovereignty
The laboratory has a specific and sustained focus on extracting and processing strategic metals from primary and secondary sources. Given India's limited primary resources for most strategic metals, research emphasises extraction from wastes, alongside some exploitation of low-grade indigenous resources. NML developed and commercialised a superior technology for tungsten recovery from scraps. Indigenous technologies for sodium and gadolinium (essential for the atomic energy programme) were successfully developed, with sodium production being scaled up by industry. High purity gadolinium was produced by fused salt electrolysis. NML is involved in lithium extraction from both primary and secondary resources (end-of-life batteries) with significant success. Substantial efforts are also made in Rare Earth element recovery from urban ores and strategic metal valorisation from industrial wastes. A dedicated urban ore recycling centre is operational, and several technology transfers for extracting lithium, cobalt, nickel, and rare earth elements from urban wastes have occurred recently.
Functional Materials
Several new alloys and materials have been developed based on the needs of clients and collaborators. Biomimetic products for bio-applications have been commercialised. Advanced coatings for aerospace multinationals have been developed with green protocols. Amorphous alloys have been developed and used in sensors. Current focus areas include 2D materials, MXenes, and magnetic shape memory alloys. Various ceramic and metallic bio-implant materials have been developed and commercialised. Further, NML’s contribution in graphene research is noteworthy. CSIR-NML's graphene activities began in 2012. The distinctive production methods, like pyrolysing carbon waste and incorporating collagen into graphite, drew in both domestic and foreign businesses. Scientist at NML created a transparent conducting electrode and corrosion-resistant coating material in partnership with Tata Steel as part of a sponsored project. These findings led to the 2015 Tata Innovista Award from Tata Sons and the 2016 APEX TQM RECOGNITION AWARD by Tata Steel. CSIR-NML also demonstrated that the collagen-based exfoliated graphene composite is suitable for energy devices, particularly batteries and super-capacitors under the sponsored project.
Structural Health Monitoring- from Manual to Remote Sensing
The laboratory is a leading organisation in structural health monitoring (SHM) due to its excellent facilities and expertise in materials characterisation and Non-Destructive Evaluation. CSIR-NML is a leader in SHM of critical industrial components, remaining life assessments, and failure investigations, having completed over three hundred projects with a diverse clientele. Research in the area of SHM at CSIR-NML has increasingly focused on designing and developing tailor-made sensing devices and sensors for industrial applications to reduce dependence on expensive imports. This includes an annealing simulator, MagStar, MagSys, MagRays for microstructural damage detection, FlawGuard and Zincometer for real time quality assessment of steel wires. CSIR-NML in collaboration with CSIR-CGCRI has led to applications of Fibre Bragg Grating (FBG) sensors, including temperature profiling of continuous casting moulds and successful implementations for breakout detection in billet casters. For this technology, CSIR-NML bagged the Tata Innovista Award by Tata Sons in 2022 in the Most Innovative Partner category as a partner of Tata Steel. Several technologies have been licensed and also implemented in the industry.
SCIENTIFIC SOCIAL RESPONSIBILITY - NML’s Science for Society
Assisting Artisans
While the brass-ware artisans across the country were in a crisis because of stiff competition from China, scientists from NML come up for rescue as a part of their scientific social responsibilities. Moreover, the home based traditional pit furnaces used by the artisans were fuel inefficient and polluting. As part of a National Innovation Council initiative, CSIR-NML developed a cost effective, fuel efficient and eco-friendly coke based brass melting furnace for the metal artisans utilising waste heat recuperating system and arresting suspended particulate matter (SPM) inside the pit. A few such furnaces were installed in Moradabad, Uttar Pradesh, in Pipali and Balasore, Odisha. Simultaneous efforts were on to enhance awareness and training of the artisans. CSIR-NML also developed an efficient, low cost anti-tarnishing lacquer to prevent tarnishing and to maintain the metallic cluster of brass handicrafts. The developed lacquer is both technically and cost-wise superior to the lacquers available in the market. The technology has been transferred to a private entrepreneur for its commercial production. CSIR-NML was also entrusted with the responsibility to generate detailed project reports (DPRs) for multiple brass and silver artisan clusters in West Bengal, which have been completed successfully.
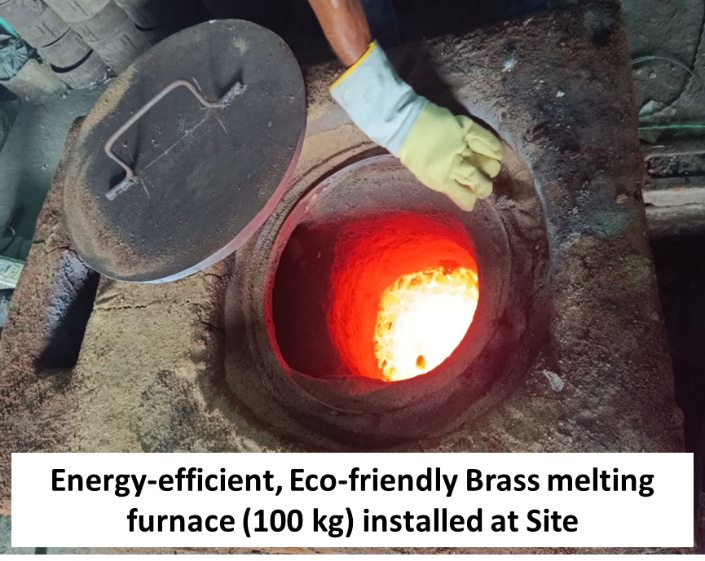
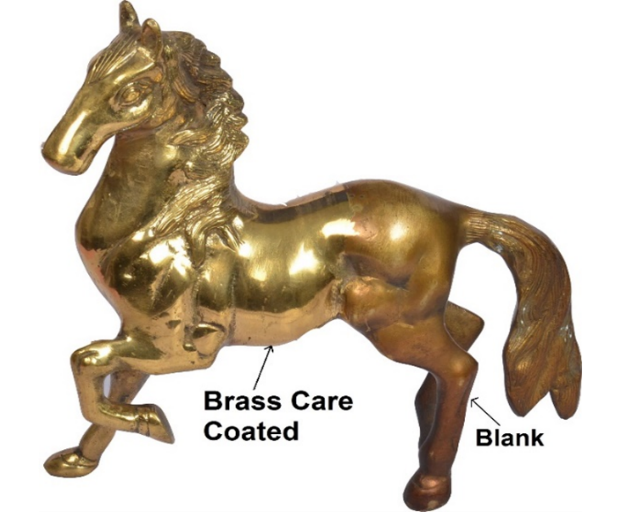